Rigorous Raw Material Inspection: Ensuring Impeccable Quality and Compliance in Manufacturing
Raw material inspection is a vital component of quality control in any manufacturing or production process. It involves assessing the quality and suitability of incoming raw materials before they are used in the production line. The purpose of the raw material inspection is to ensure that the materials meet the required specifications and comply with quality standards.
During the raw material inspection process, several key activities take place:
- Visual examination: The inspector visually inspects the raw materials to identify any visible defects, such as physical damage, discoloration, or contamination. This initial visual examination helps to identify obvious issues that may affect the quality or performance of the final product.
- Sampling: The inspector takes representative samples from the incoming batch of raw materials. The samples are selected in a manner that ensures they are a true reflection of the entire batch. These samples will undergo further testing and analysis to determine their quality and conformity to specifications.
- Testing and analysis: The collected samples are subjected to various tests and analyses, depending on the nature of the raw materials and the specific quality requirements. These tests may include measurements of physical properties, chemical composition analysis, mechanical tests, or any other relevant assessments to assess the quality and suitability of the materials.
- Documentation and record-keeping: The results of the raw material inspection, including test data, analysis reports, and any other relevant information, are documented and maintained as records. These records serve as evidence of compliance and can be used for traceability, audits, or future reference.
- Acceptance or rejection: Based on the inspection results, the raw materials are either accepted or rejected. If the materials meet the required specifications and quality standards, they are accepted for use in the production process. On the other hand, if the materials do not meet the criteria, they are rejected, and appropriate actions are taken, such as returning the materials to the supplier or initiating corrective measures.
Raw material inspection plays a critical role in ensuring that the production process starts with high-quality materials. It helps prevent defects, minimize waste, and maintain consistency in the final product. By implementing a robust raw material inspection process, manufacturers can enhance product quality, meet customer expectations, and comply with relevant industry standards and regulations.
Moreover, Raw material inspection is a crucial aspect of the ISO 9001 quality management system. ISO 9001 sets the international standard for quality management systems and provides guidelines for organizations to establish and maintain effective quality control processes. The specific requirements for raw material inspection under ISO 9001 include:
- Criteria for acceptance: ISO 9001 requires organizations to establish criteria for accepting or rejecting raw materials based on their quality and conformance to specified requirements. These criteria should be defined in terms of measurable characteristics, such as chemical composition, physical properties, dimensions, or any other relevant parameters.
- Inspection process: ISO 9001 requires organizations to implement an inspection process for raw materials. This process should be designed to ensure that incoming raw materials are thoroughly inspected to verify their compliance with the defined acceptance criteria. The inspection process may involve visual inspection, testing, sampling, or any other suitable method to assess the quality of the raw materials.
- Identification and traceability: ISO 9001 emphasizes the importance of identifying and tracing raw materials throughout the production process. Organizations must establish procedures to ensure that raw materials are appropriately identified, labeled, and recorded to maintain traceability. This helps in identifying the source and quality of the raw materials in case of any issues or non-conformities.
- Non-conforming materials: ISO 9001 requires organizations to have processes in place to address non-conforming raw materials. If a raw material does not meet the defined acceptance criteria, it should be appropriately identified, segregated, and documented as non-conforming. The organization must determine the necessary actions, such as rejection, rework, or supplier notification, to address the non-conformance.
- Records and documentation: ISO 9001 emphasizes the importance of maintaining records of raw material inspections. Organizations must establish procedures to document and retain inspection results, including details of accepted and rejected raw materials, inspection methods used, and any additional relevant information. These records serve as evidence of compliance and can be used for traceability, audits, or other quality management purposes.
By adhering to these ISO 9001 requirements for raw material inspection, organizations can ensure that only conforming raw materials are used in their production processes. This helps to maintain consistent product quality, reduce waste and rework, and meet customer requirements and satisfaction. For further inquiries, please feel free to Contact Us.
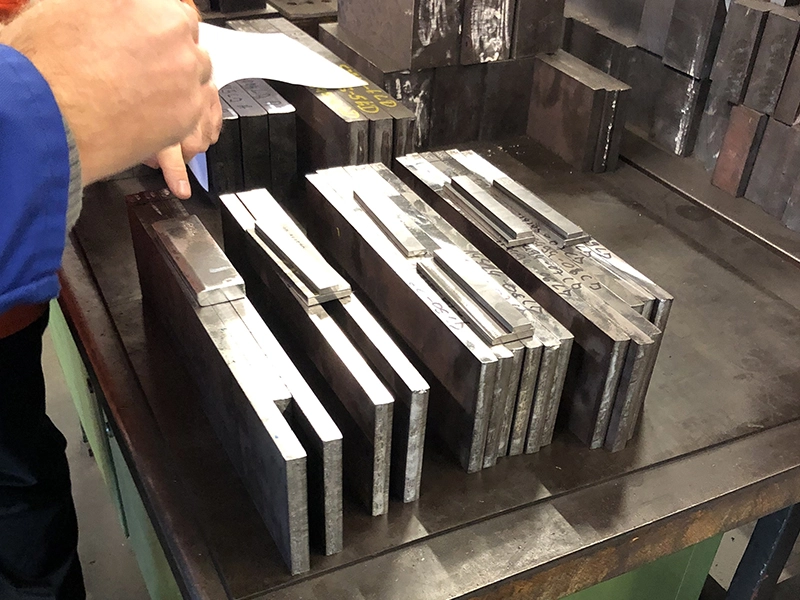

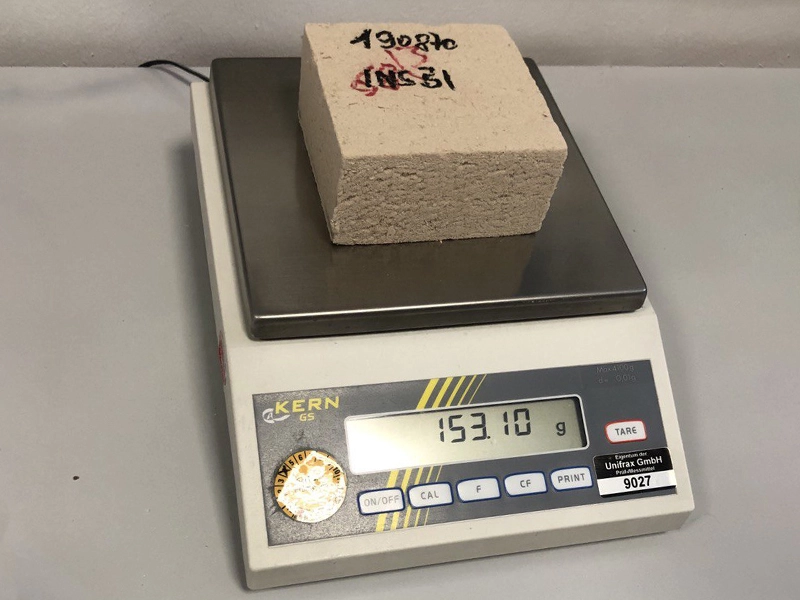