Final Inspection: A Critical Step for Product Quality and Customer Satisfaction
Final inspection is the last stage in a manufacturing or production process, where the finished product is inspected to ensure it meets the required quality standards and specifications. The purpose of the final inspection is to identify any defects, errors, or deviations that may have occurred during the manufacturing process and to ensure that the product is safe, functional, and meets customer expectations.
The final inspection process typically involves a series of checks and tests, including visual inspection, measurement, functional testing, and documentation review. The specific requirements for final inspection will depend on the type of product being manufactured and the industry standards and regulations that apply.
Visual inspection involves a thorough examination of the product’s appearance and surface finish to ensure it is free from defects such as scratches, dents, or cracks. Measurement tests may include verifying dimensions, weight, or material properties against specified tolerances.
Functional testing involves checking the product’s performance against specific requirements, such as load testing, endurance testing (Soak testing), or other tests that evaluate the product’s ability to perform its intended function.
Documentation review involves checking that all required documentation, including quality records, test reports, and other relevant documentation, is complete and accurate.
If any defects or deviations are identified during the final inspection process, appropriate corrective actions will be taken to rectify the issue before the product is released for shipment or use. Final inspection is a critical step in ensuring the quality and reliability of the product, and it is essential to the success of the manufacturing process and customer satisfaction.
For further inquiries, please feel free to Contact Us.
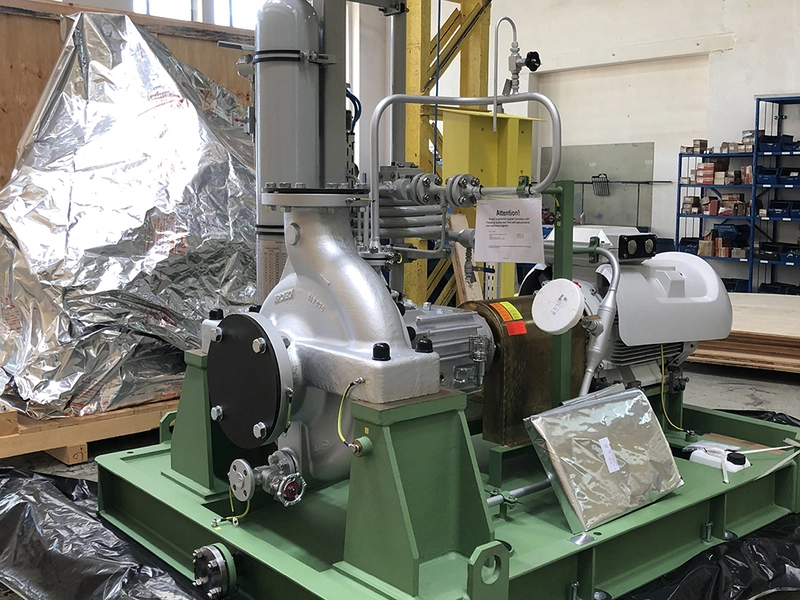
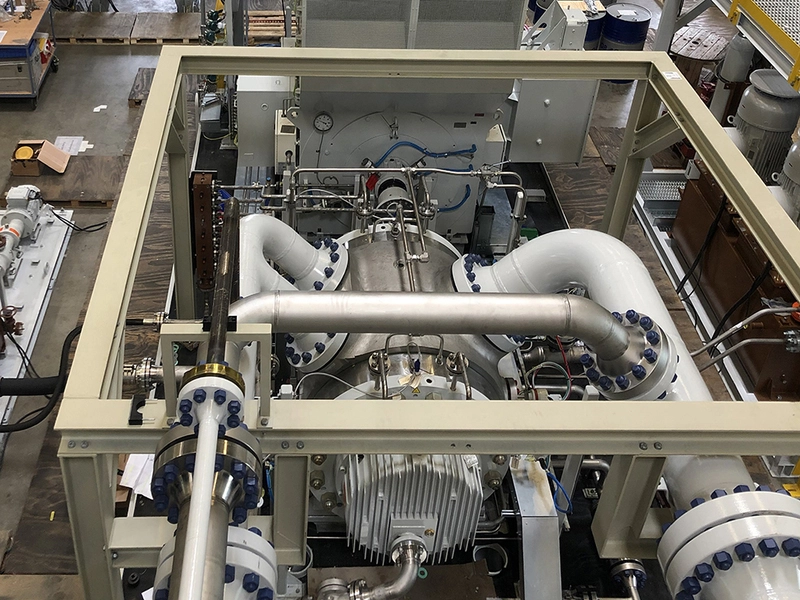
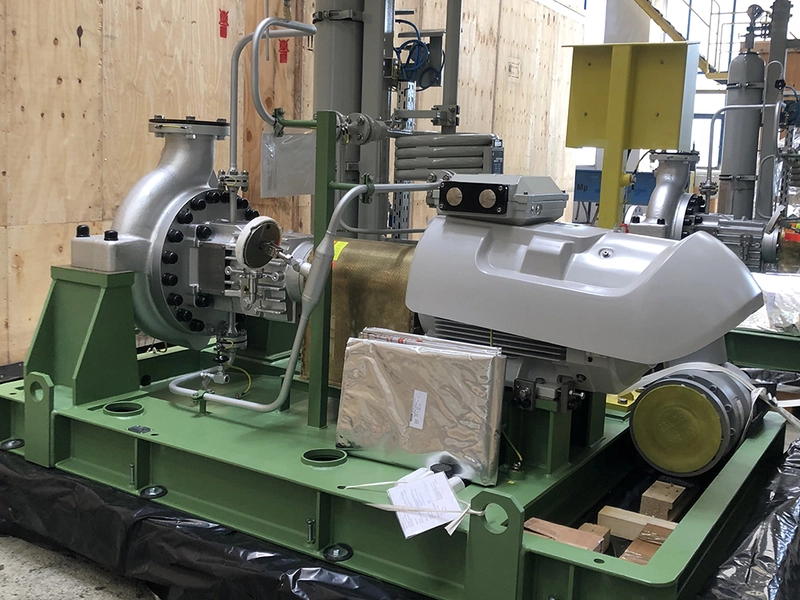