Ensuring Safety and Reliability: The Importance of Electrical Testing in Systems and Equipment
Electrical testing is an essential aspect of ensuring the safety and reliability of electrical systems, components, and devices. It involves evaluating the electrical properties of materials and systems, such as voltage, current, resistance, capacitance, and impedance, among others. Electrical testing can help detect defects, malfunctions, or inconsistencies in electrical equipment, identify potential hazards, and ensure compliance with regulatory and safety standards.
Electrical testing encompasses a wide range of techniques and methods, such as insulation resistance testing, continuity testing, voltage testing, and ground resistance testing, among others. These tests can be performed manually using handheld devices, or automated using computerized testing equipment.
During the Factory Acceptance Test (FAT), electrical testing is performed to verify the proper functioning and performance of electrical equipment and systems. Electrical testing is typically carried out under various load conditions and environmental factors to simulate real-world operating conditions. The electrical tests performed during FAT may include voltage and current measurements, insulation resistance testing, ground resistance testing, and circuit breaker testing, among others.
In addition to the electrical tests, FAT may also involve other tests, such as mechanical testing, visual inspection, and software testing, among others, to ensure that the equipment and systems meet the required specifications and quality standards. Once the testing is completed, a FAT report is generated, which includes the test results, any defects or issues identified, and recommendations for corrective actions.
- Voltage Testing: This test is performed to verify the correct voltage levels of electrical equipment. It is typically performed by measuring the voltage across various components and verifying that it is within the specified range.
- Current Testing: This test is performed to verify that electrical equipment is drawing the correct amount of current. It is typically performed by measuring the current flow through the equipment and comparing it to the specified values.
- Insulation Resistance Testing: This test is performed to determine the electrical insulation resistance of the equipment. It helps to detect any insulation faults or leaks that may cause safety hazards or malfunctions.
- Ground Resistance Testing: This test is performed to measure the resistance of the ground connections. It helps to identify any issues with grounding that may cause electrical hazards or malfunctions.
- Continuity Testing: This test is performed to check the continuity of electrical circuits. It helps to identify any open circuits or shorts that may cause malfunctions.
- Power Factor Testing: This test is performed to measure the power factor of the equipment. It helps to identify any issues with power factor that may cause inefficient or unstable operation.
- Circuit Breaker Testing: This test is performed to ensure that circuit breakers are functioning correctly. It helps to verify that the circuit breakers trip at the appropriate current levels and prevent damage to the equipment or electrical systems.
- Load Testing: This test is performed to simulate real-world operating conditions and verify that the equipment can handle the required loads. It involves subjecting the equipment to the maximum loads that it is designed to handle and monitoring its performance.
- Lightning testing: also known as surge testing, is conducted to assess the resilience of electrical and electronic equipment against the damaging effects of lightning strikes or electrical surges. Lightning is a natural atmospheric discharge of electricity that can induce high-voltage transients or surges in electrical systems. These surges can cause equipment failures, component damage, or even safety hazards. The purpose of lightning testing is to evaluate the ability of equipment to withstand and mitigate the effects of lightning-induced surges. The tests are typically performed in accordance with relevant standards, such as IEC 61000-4-5. Lightning tests involve subjecting the equipment to simulated lightning surges of varying magnitudes and waveforms to simulate the effects of actual lightning strikes.
These tests can be performed manually using handheld devices or automated using computerized testing equipment. By conducting these tests during FAT or in general, manufacturers and customers can ensure that the electrical equipment and systems are safe, reliable, and meet the required specifications and standards.
We are here to assist you further, so please don’t hesitate to contact us for any additional inquiries.
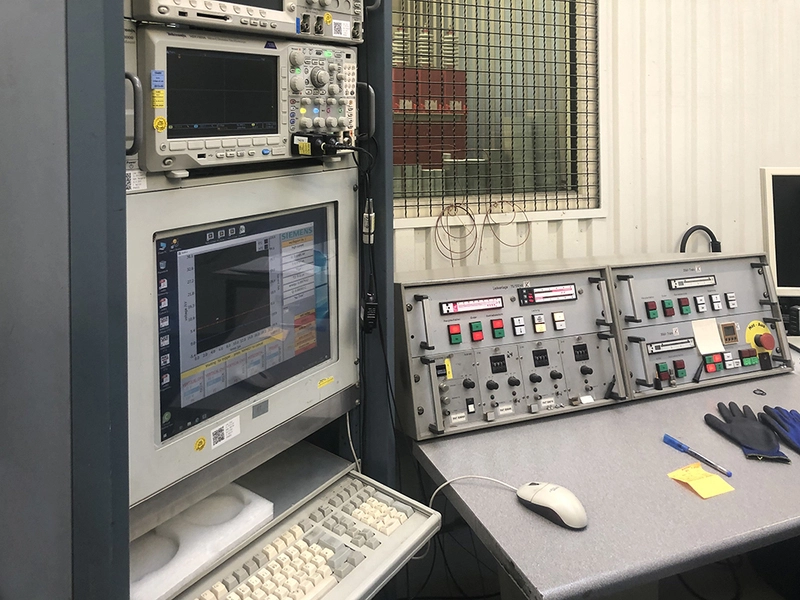

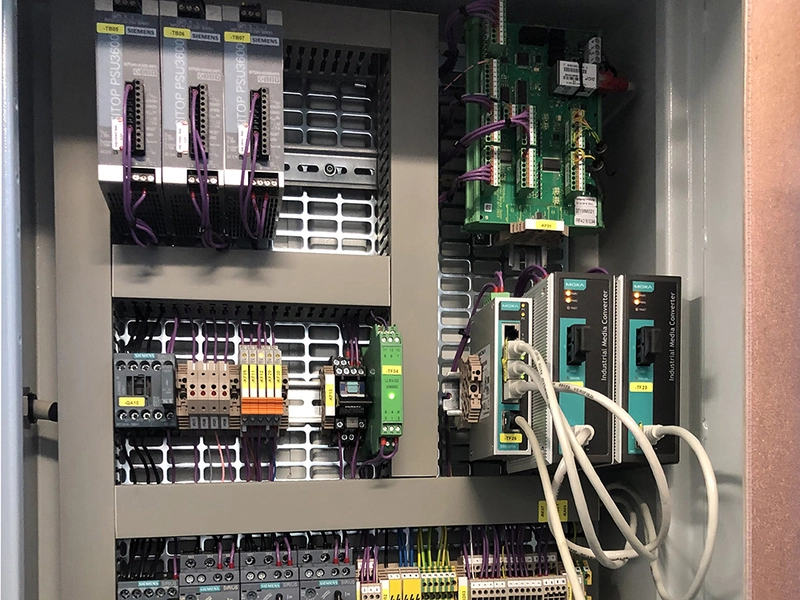